Do you think that your manufacturing process is as efficient as it could be? If not, then you should read this guide to understand how you can apply the Six Sigma Methodology to your manufacturing processes to significantly enhance your productivity.
What is Six Sigma Methodology?
In simple terms, Six Sigma is a set of tools and techniques designed to improve the quality of process outputs by identifying and removing the causes of errors and minimizing variability in manufacturing and business processes.
To break it down further, think of Six Sigma as a measure of quality that strives for near perfection. It’s a structured, data-driven approach to problem-solving. The goal is to improve your operations so much that you’ll have fewer than 3.4 defects per million opportunities. That’s where the term ‘Six Sigma’ comes from.
In practice, this means looking at what you’re doing in your manufacturing process, figuring out where things go wrong, and then finding solutions to these problems. This not only helps to improve the quality of your products but also saves you time and money, making your business more efficient.
Why is Six Sigma so Important for Manufacturing?
Firstly, it’s all about improving quality. By minimizing defects and inconsistencies, manufacturers can produce products that meet customer expectations more reliably. This leads to happier customers who are more likely to stick around and recommend your products to others.
Secondly, Six Sigma helps save money. It might seem counterintuitive, but spending time and resources on improving processes can lead to significant savings in the long run. By reducing waste and improving efficiency, you can cut costs without compromising on the quality of your products.
Lastly, Six Sigma provides a clear roadmap for improvement. It’s not just about identifying problems, but also providing structured, data-driven methods to solve them. This makes it easier for manufacturers to make consistent, ongoing improvements to their processes, leading to long-term success.
In other words, Six Sigma is important because it promotes high quality, cost savings, and continuous improvement in manufacturing.
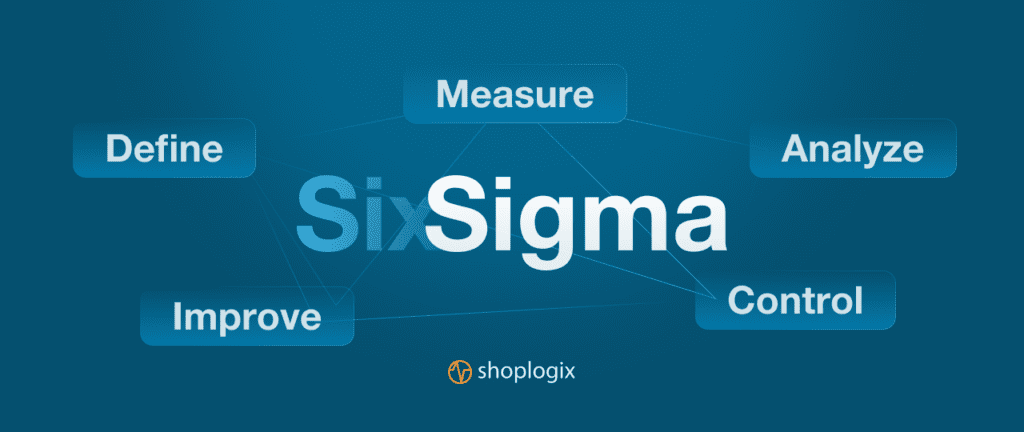
What does the Six Sigma Process look like and How can Manufacturers Implement It?
The Six Sigma process follows a systematic approach that involves five key steps, often remembered by the acronym DMAIC: Define, Measure, Analyze, Improve, and Control.
- Define: This step involves clearly identifying the problem or issue that needs to be addressed. It’s about understanding the goals of the project and what needs to be achieved.
- Measure: In this stage, you gather data related to the problem identified in the first step. This could involve measuring current performance levels, identifying relevant metrics, or collecting other relevant data.
- Analyze: Once you have your data, the next step is to analyze it to identify patterns, trends, or anomalies. The goal here is to figure out where the problems are and why they’re happening.
- Improve: After analyzing the data, you then develop solutions to address the issues identified. This could involve making changes to processes, implementing new procedures, or taking other steps to improve performance.
- Control: The final step is to monitor the situation to ensure that the improvements are sustained. This might involve ongoing data collection, regular reviews, or other forms of monitoring and control.
Manufacturers can implement Six Sigma by first understanding their processes and identifying areas where improvements can be made. They can then use the DMAIC method to systematically address these areas, using data to drive their decision-making and ensure that changes lead to real improvements.
One important thing to note is that implementing Six Sigma often requires a cultural shift within the organization. It requires buy-in from all levels of the organization and a commitment to continuous improvement. Therefore, training and education are often key components of a successful Six Sigma implementation.
Key Six Sigma Principles Explained
Six Sigma methodology is built around a set of principles that guide its implementation and use. Here’s a breakdown of the key principles:
- Focus on the Customer: Six Sigma begins with the end-user in mind. Manufacturers aim to understand the needs and expectations of their customers, using this insight to drive process improvements.
- Data-Driven Decisions: Six Sigma is rooted in data and facts. Decisions aren’t based on assumptions or gut feelings, but instead on solid, reliable information. This enables manufacturers to make informed choices that enhance productivity and efficiency.
- Process-Oriented Approach: Six Sigma recognizes that outcomes are the result of processes. By focusing on refining and optimizing these processes, manufacturers can improve overall results.
- Proactive Management: Rather than waiting for issues to occur, Six Sigma encourages proactive problem-solving. It’s about identifying potential problems before they escalate into larger issues, ensuring smooth operations and less disruption.
- Collaboration and Teamwork: Implementing Six Sigma is a team effort. It involves participation from all levels and areas of an organization, fostering a collaborative environment where everyone works together to identify and solve problems.
- Continuous Improvement: Six Sigma isn’t a one-and-done solution. It emphasizes continuous, ongoing improvements to processes and performance, fostering a culture of constant growth and development.
By adhering to these principles, manufacturers can effectively implement the Six Sigma methodology, driving improvements in quality, efficiency, and customer satisfaction.
Benefits of Six Sigma Methodology
Six Sigma offers numerous benefits, especially for manufacturers. It provides a structured, data-driven methodology for eliminating defects and reducing variability in processes. This can lead to significant improvements in quality, efficiency, and customer satisfaction.
By focusing on the customer, Six Sigma helps manufacturers to better align their products and services with market needs, leading to increased competitiveness. Furthermore, the emphasis on proactive management and continuous improvement fosters a culture of excellence that can drive long-term success.
Why it Might Not Work for You
Despite its many advantages, Six Sigma may not be the right fit for every organization. Implementation requires a significant investment of time and resources, which some smaller businesses may not be able to afford. It also demands a high level of commitment from all levels of the organization, and without this buy-in, efforts may fall flat.
Moreover, Six Sigma’s focus on reducing variability and eliminating defects might not align with the strategic objectives of firms that prioritize innovation or speed to market over consistent quality. Lastly, if not properly managed, the data-driven nature of Six Sigma can lead to an over-reliance on quantitative measures at the expense of qualitative insights.
What You Should do Next
Explore the Shoplogix Blog
Now that you know more about the Six Sigma Methodology, why not check out our other blog posts? It’s full of useful articles, professional advice, and updates on the latest trends that can help keep your operations up to date. Take a look and find out more about what’s happening in your industry. [Read More]
Request a Demo
Learn more about how our product, Smart Factory Suite, can drive productivity and overall equipment effectiveness (OEE) across your manufacturing floor. Schedule a meeting with a member of the Shoplogix team to learn more about our solutions and align them with your manufacturing data and technology needs. [Request Demo]