Are you familiar with the 5S in lean manufacturing? It’s a methodology many successful manufacturers employ to stay efficient and productive. Read on to discover how this approach can significantly improve your manufacturing process.
What is the 5S Methodology?
The essence of the 5S methodology can be encapsulated in the saying, “Everything has a place, and everything is in its place.’
You might be familiar with the «KonMari» system, a home organization technique popularized by Marie Kondo, which transforms disorganized households into streamlined and orderly living spaces. The principles of 5S share similarities with KonMari. However, it’s an oversimplification to say that 5S is merely about tidying up. Much like stating that the key to successful manufacturing is speed, it doesn’t capture the entire picture.
The Genesis of 5S: The concept of 5S originated from five Japanese terms:
- Seiri
- Seiton
- Seisou
- Seiketsu
- Shitsuke
The 5S terms translate to the following in English:
- Sort (Seiri): Remove what isn’t necessary.
- Straighten (Seiton): Arrange what remains after sorting.
- Shine (Seisou): Cleanse and inspect the workspace.
- Standardize (Seiketsu): Establish standards for 5S.
- Sustain (Shitsuke): Maintain the consistent application of the 5S standards.
At its heart, these 5S practices foster the discipline required for significant and ongoing improvement by establishing (and maintaining) productive and efficient workspaces.
What is Sort (Seiri)?
The ‘Sort’ step in the process involves distinguishing between necessary items in your workspace and those that are potentially unneeded, relocating the latter to a designated ‘red tag’ holding area.
Why Manufacturers Need it
This step enhances your workspace productivity by eliminating unnecessary clutter and distractions. It’s also the initial stage in freeing up space for other uses.
How to Implement it
Distinguish between essential items (like tools, parts, and materials) and those that are not required. We suggest classifying items into four groups:
- Items Required in this Workspace: These are the items you frequently use within this specific workspace, hence they will remain here.
- Items Needed in a Different Workspace: These are typically misplaced items. If an item is utilized in another workspace, relocate it to the appropriate area by handing it over to the team member in charge of that workspace.
- Potentially Required Items: For items you’re uncertain about, employ the 5S ‘red tag’ system. Label such items with red tags, which should include, at the very least, the tagger’s name, the reason for its potential redundancy, a proposed review date, and the name of the manager who must approve its disposal. Transport the item to a designated red tag holding area, which should be arranged by review month for easy management.
- Unnecessary Items: These are items that you are absolutely certain are not needed. They should be immediately discarded, recycled, donated, or sold if they are in good condition.
Common Examples of Sort
- Eliminate unnecessary items, or ‘muda’, from your workspace.
- Use the 5S red tag system to dispose of outdated or broken parts.
- Ensure materials and papers are recycled responsibly.
- Distinguish between tools used daily and those needed for special cases.
- Prevent cluttering your workspace with surplus materials.
- Establish a designated area outside of the workspace for storing duplicate materials, tools, and components.
What is Straighten (Seiton)?
The ‘Straighten’ phase meticulously arranges the items left post-sorting, ensuring frequently used items are readily accessible and each item has a distinct, easy-to-locate place.
Why Manufacturers Need it
‘Straighten’ ensures each item has a designated spot where it can be effortlessly located and returned. This reduces unnecessary movement by positioning items in more user-friendly locations. As the second step in the process, ‘Straighten’ aids in freeing up space that can be strategically utilized to enhance production efficiency.
How Implement it
Once the sorting phase is complete, it’s time to strategize on organization. Here’s a suggested approach:
- Prioritize Accessibility for Frequently Used Items: Minimizing waste from excessive motion can be achieved by having commonly used items within a convenient reach.
- Categorize Similar Items: Group the remaining items into sensible categories and contemplate the optimal method to organize and store each category.
- Implement Visual Cues: For each category, determine the most effective way to indicate if an item is missing or out of place. A timeless example is the use of a shadow board for tools.
- Consider using Containers; If suitable for the type of item, organizing it within a container might be useful.
- Employ Labeling: For larger items that cannot fit into a container, consider outlining a designated space and attaching a label both to the item and the outlined area.
- Remain Adaptable: Your initial ‘Straighten’ attempt will likely yield considerable improvement, but there may be overlooked opportunities for enhancement. Schedule a 5S team meeting focused on further straightening after one and two weeks, and brainstorm additional improvements during your initial implementation.
Common Examples of Straighten
- Assign a unique «spot» for each item.
- Utilize color schemes as a means to bring structure and significance.
- Incorporate shadow boards and additional visual cues on the production floor.
- Allocate a specific surface or space solely for shadow boxes and tool storage.
- Reserve another surface or area exclusively for work-related tasks.
What is Shine (Seisou)?
The ‘Shine’ phase enhances the workspace by guaranteeing that all tools, equipment, and other items are meticulously cleaned and examined. It may also encompass regular upkeep of machinery, which seamlessly integrates it with Total Productive Maintenance (TPM).
Why Manufacturers Need it
‘Shine’ makes the workplace better by giving workers more control over their work area. It also helps them spot problems before they mess up the work flow. For example, in a clean workspace, it’s much easier to see things like leaks, spills, metal bits from unexpected damage, tiny cracks in equipment, and so on.
How to Implement it
Once you’ve tidied up the items, it’s time to upgrade your workspace by cleaning, inspecting and, in some cases, carrying out regular maintenance. Here’s our suggestion:
- Embrace the Cleaning Spirit: Utilize suitable cleaners and cleaning tools to make your workspace shine. Every sweep, mop, brush, wipe, wash, and wax should aim to restore your workspace to its prime condition. Channel your inner Miyagi.
- Identify the Origin: The main idea behind this 5S step is «clean to understand». If there are signs of leaks, spills, or unexpected debris, make an effort to identify the cause. It could be an early indication of a future issue.
- Check Every Item: After cleaning each item, spend a moment to check its condition. Does it need an upgrade, maintenance, or repair?
Common Examples of Straighten
- Clean your equipment thoroughly.
- Check the condition of your tools for any wear and tear.
- Take apart bigger items to assess the condition of their components.
- Look into a persistent area of dirt or disorder.
- Always adhere to the correct cleaning processes to avoid causing harm to your equipment.
What is Standardize (Seiketsu)?
The Standardize phase acts as a link between the initial three 5S steps (Sort, Straighten, Shine) and the final step (Sustain). In this phase, your aim should be to document the best methods for 5S as standard procedures for your team.
Why Manufacturers Need it
The Standardize phase ensures the repeatability of the 5S process. It evolves 5S from a standalone project to a set of activities that can be consistently replicated.
How toImplement it
It’s vital to ensure that your diligent efforts continue to yield benefits in the long run. Establish future guidelines using a well-documented 5S process. Here are some suggestions:
- Collaborative Documentation: Engage two team members for every 5S task – one to perform it and the other to record it. This ensures no crucial details are overlooked.
- Emphasize the Core: We strongly advocate for simplicity and agility. Focus on capturing the essential aspects of each task without overcomplicating. This approach makes your documentation manageable.
- Opt for Checklists: Checklists are user-friendly, and shorter ones are even more so. A practical format includes a brief name for each task that acts as a quick reference, along with a more comprehensive description for training purposes.
- Streamline for Ease: Arrange your checklists based on role, shift, and frequency (daily, weekly, monthly). This organization makes the 5S process less daunting for your team.
What is Sustain (Shitsuke)?
The Sustain phase guarantees that the 5S methodology is implemented consistently. It metamorphoses your standardized 5S procedures into tasks that are routinely accomplished.
Why Manufacturers Need it
The repeated process of 5S helps to secure your success and promises continuous and lasting improvement.
How to Implement it
Once standardization is in place, it’s crucial to continually uphold those standards. Here are our suggestions:
- Establish a Timetable: Incorporate 5S methodologies as routine tasks, organized by role, shift, and frequency.
- Educate via Practical Examples: Train employees on the execution of 5S tasks through hands-on demonstrations and instruction. By illustrating what is anticipated from them, employees will be better equipped to perform tasks independently.
- Oversee Until Independence is Achieved: Following the initial 5S training for employees, provide supportive supervision as they develop these new habits. Missteps or deviations are common, so kindly and constructively provide corrections when required.
- Evolve as Required: When providing or receiving feedback on tasks, identify opportunities for adjustments to enhance efficiency and ease of tasks. Remember, standardized work is intended to be a dynamic document, not a static one.
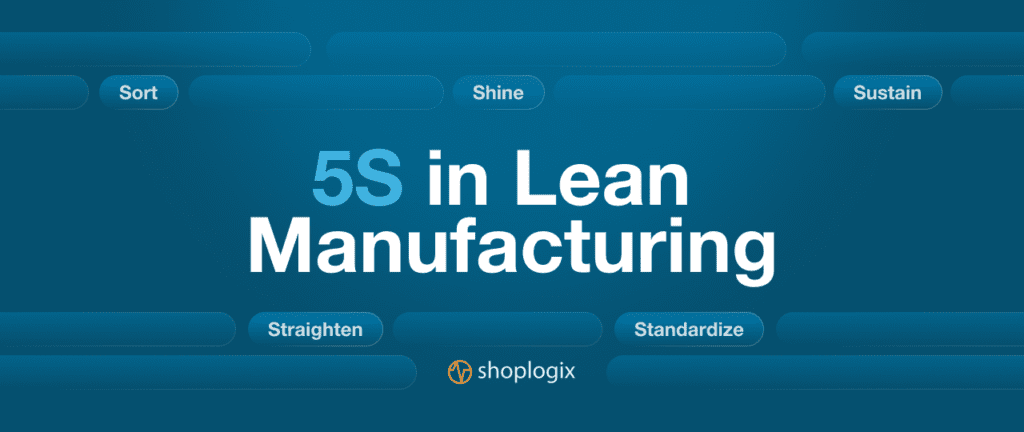
What Exactly is 5S in Lean Manufacturing?
When applied to lean manufacturing, the 5S methodology forms the bedrock of a well-organized, spotless, and high-functioning work environment. It’s a systematic approach that provides a foundation for ongoing improvement, waste minimization, and performance optimization.
For manufacturers, the 5S system is crucial as it directly contributes to operational efficiency and productivity. By helping to identify and eliminate waste, it streamlines production processes and reduces costs. For instance, by sorting and straightening, manufacturers can ensure every tool and piece of equipment is kept in its designated place, reducing the time spent searching for them.
The ‘shine’ aspect ensures that the workplace is not only clean but also has regular maintenance performed, preventing machine downtime due to unexpected breakdowns. Standardizing processes leads to consistent quality in products, reducing rework and returns. Sustaining the practices ensures the benefits of 5S are not short-lived but become part of the company’s culture.
Without 5S, manufacturers might struggle with inefficiencies, errors, and safety issues. A cluttered workspace can lead to mistakes, lost items, and accidents. Inconsistencies in the way tasks are performed can result in product quality variations. If the 5S practices are not sustained, the workplace could easily revert back to its original state, negating any improvements made.
Pros and Cons of 5S in Lean Manufacturing
Why Manufacturers Should Take Advantage of 5S
- Implementing the 5S methodology in lean manufacturing brings several benefits.
- It can greatly enhance productivity by organizing the workspace and ensuring everything has its place, reducing time spent searching for tools or materials.
- This leads to smoother and more efficient processes.
- Another benefit is cost reduction, as the 5S method helps manufacturers identify and eliminate waste.
- This avoidance of unnecessary expenses helps increase profit margins.
- The 5S approach also encourages employees to take ownership of their workspace.
- This fosters a sense of responsibility and involvement, which can improve morale and productivity.
- Lastly, creating a clean, well-organized, and standardized work environment reduces the likelihood of accidents, promoting a safer workplace.
Challenges of 5S in Lean Manufacturing you Should Know
- While the 5S methodology offers many benefits to lean manufacturing, it also presents several challenges.
- A significant issue arises when 5S is perceived as just another tool, not a crucial part of the company’s culture. This perception can hinder long-term lean transformation goals.
- Another potential obstacle is overemphasis on the «5S first» approach. If treated as a standalone program, it might divert attention from other important aspects of lean manufacturing.
- Maintaining the 5S practices over time can be difficult. It requires ongoing commitment and discipline from all employees, which can be challenging to maintain without continuous support and reinforcement.
- Finally, while 5S can lead to immediate improvements in efficiency and organization, it might not address deeper, systemic issues. Manufacturers must ensure that 5S is integrated with other lean practices for comprehensive and sustainable success.
What You Should do Next
Explore the Shoplogix Blog
Now that you’re done here, why not check out our other blog posts? It’s full of useful articles, professional advice, and updates on the latest trends that can help keep your operations up to date. Take a look and find out more about what’s happening in your industry.
Request a Demo
Learn more about how our product, Smart Factory Suite, can drive productivity and overall equipment effectiveness (OEE) across your manufacturing floor. Schedule a meeting with a member of the Shoplogix team to learn more about our solutions and align them with your manufacturing data and technology needs.