Continuous improvement software is the cornerstone of long-lasting success, going beyond quick fixes and instant solutions. Because everyone is looking for one and done solutions for instant success. Whether it’s magic diet pills promising to lose 10 pounds in a week or turnkey solutions that are the “answer” to instant growth for your enterprise, people are drawn to the idea of overnight results. Here’s the thing though, the road to success is always under construction.
Even when you think you’ve finished building it, there’s always room to expand and bumps to flatten. The long-term success of larger goals must be supported by continuous improvement software in order to gain sustainable results. This mindset, led by the manufacturing world, is better known as kaizen.
What is ‘Kaizen’?
Kaizen is a term derived from two Japanese words: «Kai,» meaning «change,» and «Zen,» which means «good.» The literal translation of Kaizen is «improvement» or «change for the better.» This philosophy is a cornerstone of lean manufacturing and digital transformation strategies.
At its core, Kaizen aims to enhance standardized activities and processes through consistent, small-scale adjustments. These incremental changes are made frequently with the ultimate objectives of reducing defects and problems, eliminating waste, and boosting productivity.
Kaizen fosters a sense of purpose and accountability among workers. It encourages them to take ownership of their roles and contribute to the overall improvement of the organization. Kaizen promotes a culture of innovation, encouraging everyone within the organization to think creatively and propose new ways to enhance efficiency and effectiveness.
The automotive giant Toyota is a prime example of Kaizen’s successful implementation. Toyota has ingrained Kaizen so deeply into its operations that all production line personnel are expected to halt the assembly line at the first sign of any abnormality. They, along with their supervisor, are then tasked with proposing an improvement to resolve the issue, thus creating what is referred to as a kaizen moment.
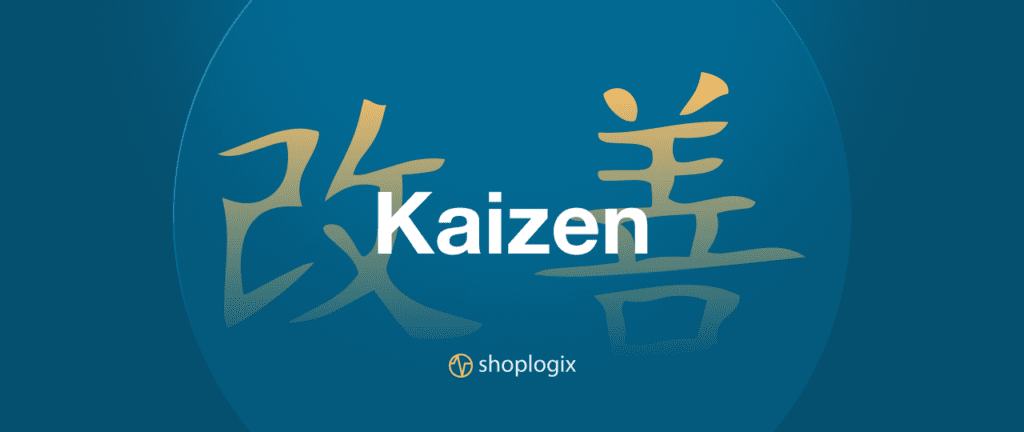
Why is Kaizen so Important?
Kaizen is fundamentally important, particularly for manufacturers, as it brings about a multitude of tangible benefits that directly impact the company’s bottom line. These advantages encompass increased productivity by optimizing processes, reduced errors and defects leading to higher quality output, shortened production times which enhance efficiency, and lower costs due to waste minimization.
Moreover, Kaizen improves the quality of both products and services, fostering customer satisfaction and loyalty. It fuels innovation by encouraging out-of-the-box thinking and problem-solving. Importantly, Kaizen also positively transforms workplace culture and boosts employee fulfillment by empowering them to contribute to the company’s continuous improvement.
Despite these significant benefits, many manufacturing companies across various sectors – including automotive to food and beverage, and consumer packaged goods (CPG) – find implementing the Kaizen philosophy challenging. The reasons for this struggle are varied and include:
- The process of manually creating, documenting, and tracking daily, weekly, and monthly improvements can be overwhelming and time-consuming without the right software to facilitate these tasks.
- Companies often find it difficult to track and identify the root cause of machine stoppages and related issues, which hinders the formation of effective kaizens.
- The lack of employee buy-in and accountability can undermine the implementation of Kaizen, as it relies on active participation from all staff levels.
- Some companies fail to recognize the long-term significance of Kaizen and its cumulative impact on overall digital transformation.
To address these challenges, Continuous Improvement Software (CI Software) comes into play. This software simplifies the implementation of Kaizen philosophy, making it more accessible and practical for organizations of all sizes and industries. CI Software streamlines the process of tracking improvements, pinpoints issues, fosters accountability, and helps quantify the impact of Kaizen on digital transformation.

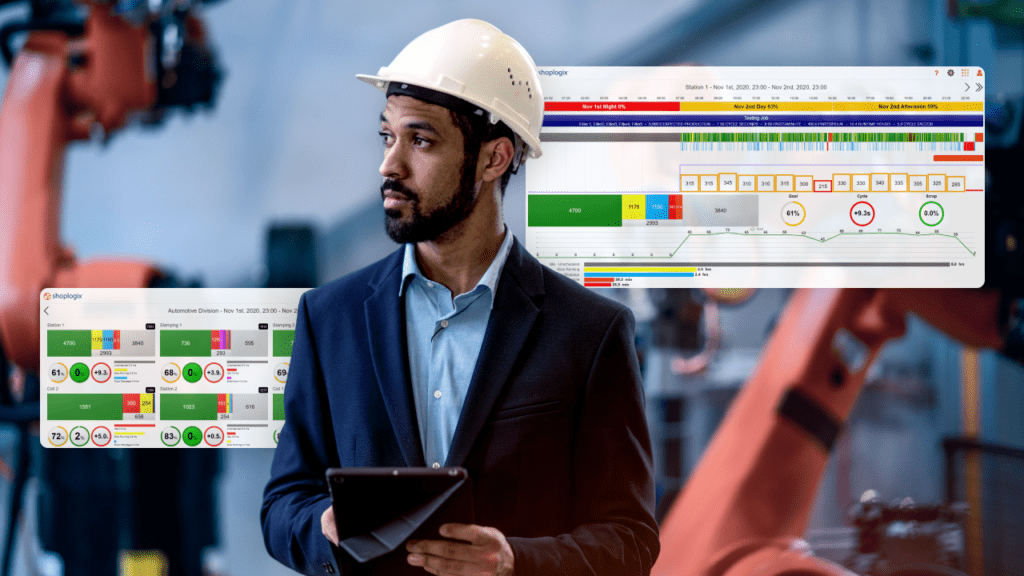
How can Continuous Improvement Software Support Your Manufacturing Kaizen?
True manufacturing software will have built-in CI modules in order for customers to make the most out of the software and ensure continued long-term and sustainable success of their digital transformation.
One such comprehensive solution is the Shoplogix Smart Factory Platform. It provides end-to-end manufacturing functionality through a variety of CI modules. Moreover, it seamlessly integrates kaizen principles into its functionality, helping manufacturers maintain and accelerate their growth trajectory.
Here are some key features of the Shoplogix platform:
1. Centralized Messaging: The platform allows for centrally controlled messages that can be disseminated at various levels – from the corporation as a whole down to individual plants, production lines, or even specific machines. This ensures consistent communication across all levels.
2. Energy Management: The platform equips users with the ability to associate power and energy costs with plant floor production metrics. This offers visibility into energy consumption at a granular level, paving the way for strategies aimed at decreasing energy costs.
3. Smart Video Integration: Through CCTV integration, the Shoplogix platform connects the whiteboard to the plant floor. This allows users to see precisely what happened at any given time, shedding light on the root causes and reasons behind inefficiencies.
4. Action Plan Tracking: The platform tracks and reports on the accountability, delivery, and status of action plans. This allows users to monitor the progress of improvements closely. (Stay tuned for more information on our new and improved Action Plan feature, coming soon!)
5. Kaizen Integration: The platform simplifies the process of defining problems identified by SLX data and root cause analysis tools. It enables task assignment and tracks improvements, making the implementation of kaizen principles more manageable and effective.
Final Thoughts
Harnessing the capabilities of the Shoplogix Smart Factory whiteboard allows manufacturers to pinpoint the root causes of production halt and downtime through direct observation on the plant floor. Subsequently, kaizens are formulated and digitally recorded within the system, eliminating the need for manual data entry and cumbersome paper trails.
The advantages of this approach are overwhelming:
- It eradicates the necessity to manually document and monitor kaizens, streamlining the process.
- It enhances the traceability of issues, making it easier to identify and address them.
- It fosters collaboration by linking multiple stakeholders through shared tasks and assignments.
- It generates kaizen reports that clearly outline problems and propose actionable steps.
- It instills a sense of accountability for the timely completion of kaizen tasks.
- It enables the tracking of kaizen progress through Shoplogix trend reports.
The Shoplogix Smart Factory platform not only improves efficiency but also promotes a culture of continuous improvement within the manufacturing sector. To fully understand the potential of this transformative platform, we invite you to schedule a demo with one of our Smart Factory Experts today!