One methodology that has proven effective in achieving this is lean manufacturing. In this blog post, we will explore seven key areas of improvement in lean manufacturing and how Shoplogix’s Smart Factory Suite can provide tailored solutions.
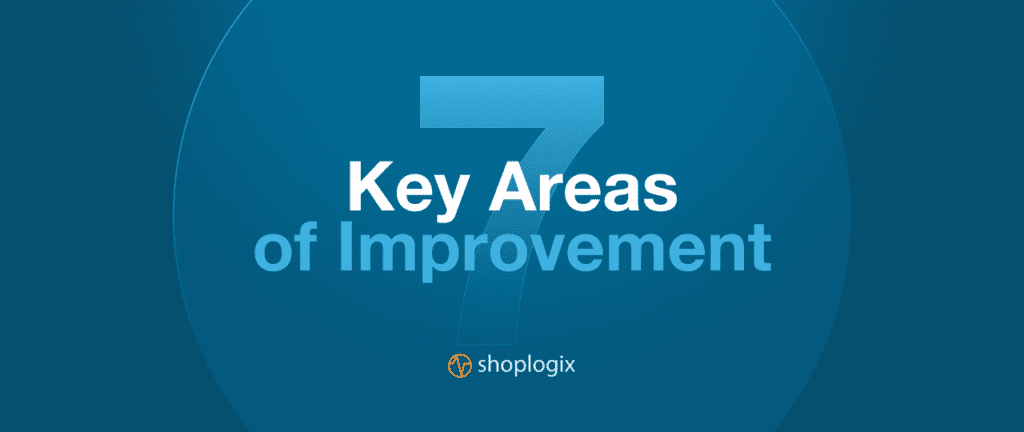
7 Key Areas of Improvement Examples
Lean manufacturing focuses on minimizing waste and maximizing productivity to deliver high-quality products efficiently. However, implementing lean manufacturing is not a one-size-fits-all process. It requires identifying and addressing specific areas of improvement.
1. Overproduction
Overproduction in a manufacturing context can be compared to an automotive factory producing more cars than it can sell. At first glance, this strategy might seem prudent, as it ensures a ready supply of vehicles for any potential surge in demand. However, the reality is that overproduction often results in excess inventory, wastage, and capital tied up in unsold products. These unsold cars take up valuable space and represent resources that could have been allocated more efficiently.
Now, suppose this automotive factory could accurately predict the number of cars they will sell each day and produce exactly that number. This would minimize waste and optimize resource allocation.
But how can such precision be achieved?
Mitigate Overproduction With Real-Time Performance Monitoring
With its real-time performance monitoring capabilities, Shoplogix serves as a highly accurate forecaster, able to gauge customer demand and help manage production schedules accordingly. It helps synchronize production with demand, effectively reducing overproduction.
For instance, if Shoplogix’s analytics point out that car sales tend to dip mid-week, the factory can adjust its production schedule, manufacturing fewer cars and conserving resources. Conversely, if there is a consistent demand surge on weekends, the factory can increase production to meet this demand, ensuring no customer is left without options.
2. Inventory
Excess inventory in the manufacturing industry is akin to a factory producing parts round the clock, even when those parts aren’t needed right away. These surplus parts, similar to overstocked items in a warehouse, not only occupy valuable space but also tie up your capital resources. Moreover, as time passes, they can become obsolete or spoil, leading to unnecessary waste.
Streamline Inventory Management With Intelligent Planning and Scheduling
With its intelligent planning and scheduling capabilities, Shoplogix empowers businesses to manage their inventory levels effectively. It’s like having a skilled operations manager who ensures that every part produced aligns with an existing demand, eliminating unnecessary production.
Shoplogix promotes a continuous flow of goods, maintaining just the right amount of stock to meet demand, without creating excess. This approach, known as a pull system, is similar to manufacturing parts precisely when they’re needed, instead of mass-producing in anticipation of potential future requirements.
3. Defects
Quality control is a key aspect of any manufacturing or production process, much like a strict supervisor ensuring every item on the assembly line meets the required standards. Defects are the unwanted «missteps» in this process. They drain resources, require additional work to correct, and can ultimately lead to unhappy customers.
Consider a car manufacturing plant. If defective parts are used in the assembly process, the car may not function properly. This could lead to costly recalls, repairs, and most importantly, disappointed customers who expected a smoothly running vehicle.
Address Defects With Shoplogix’s Quality Management
Shoplogix’s quality management module is like an eagle-eyed inspector on your production line. It helps identify and correct defects early in the process, much before the car reaches the customer.
By spotting a faulty part early, for example, a malfunctioning engine component, Shoplogix allows you to rectify the issue before it becomes a bigger problem. The faulty part can be replaced immediately, saving the time and cost of reworking an entire engine later.

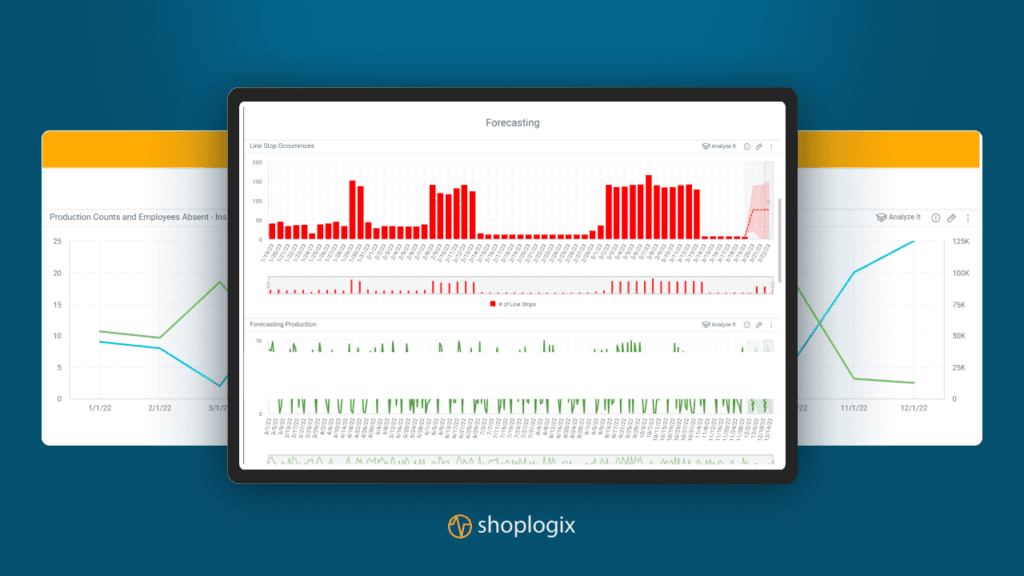
4. Motion
In manufacturing and production, motion is an important factor that directly impacts your plant’s efficiency. Unnecessary movement, whether it’s people or machines, can be likened to a worker having to walk back and forth across a large factory floor just to fetch a single tool. This inefficient use of time and energy results in wasted resources and decreased productivity.
Think about a packaging line in a factory; if the packing materials are stored at one end of the factory and the products at the other, workers would have to traverse the entire factory multiple times just to package a single item. This not only leads to unnecessary movement but also wastes valuable time that could be better utilized.
Optimize Motion With Shoplogix’s Advanced Analytics
With its advanced analytics, Shoplogix enables you to optimize your workplace layout and ergonomics, effectively minimizing unnecessary motion. Using the previous example, Shoplogix might suggest rearranging the factory so that packing materials are located next to the products. This simple change would drastically reduce the distance workers need to cover, thereby boosting productivity and saving time.
5. Over-processing
Over-processing in the manufacturing sector can be likened to an assembly line worker who spends extra time polishing a part that will be hidden from view in the final product. While the intention might be good, the additional effort doesn’t add value to the end customer but instead leads to wasted time and resources.
Imagine if this assembly line could find a way to only perform necessary tasks that add value to the final product, thus eliminating unnecessary steps and leading to a more efficient use of time and resources. The key question is how to achieve this optimal level of efficiency.
Reduce Over-processing With Shoplogix’s Process Optimization Tools
With its process optimization tools, Shoplogix acts like a smart manager who knows exactly which processes are essential and which are not. It helps simplify processes and use resources more effectively, thereby reducing waste and improving overall efficiency. This makes Shoplogix an invaluable asset for any manufacturer seeking to optimize their production process and maximize profitability.
6. Waiting
Idle time, when machines or people aren’t working, is a form of waste. This wasted time results in reduced productivity and increased costs. Now, imagine if this idle time could be minimized, with all elements of the production process working together seamlessly.
Reduce Idle Time With Real-Time Data and Predictive Analytics
With its real-time data and predictive analytics, Shoplogix ensures that every part of the production line is ready when needed. It helps better coordinate processes, reducing downtime, and ensuring a smooth, uninterrupted flow of operations.
Consider a factory that manufactures furniture. In this factory, the assembly line often comes to a standstill because the wood cutting machine takes longer than expected to prepare the necessary parts. This causes the workers and other machines on the line to wait, leading to idle time.
With Shoplogix’s real-time data, the factory can monitor the performance of the wood cutting machine and identify the causes of delay. Furthermore, the predictive analytics feature can forecast when these delays are likely to occur. Using this information, the factory can adjust its schedule, ensuring that the assembly line workers have other tasks to work on during these periods, thereby minimizing downtime.
7. Transportation
In the world of manufacturing, unnecessary transportation can be likened to taking a long, winding path when a shorter, more direct route is available. This results in wasted time, increased costs, and potential damage to products or materials.
Imagine a production process where each stage transitions smoothly to the next, akin to an efficient conveyor belt, effectively minimizing unnecessary transportation. The challenge lies in determining the best approach to achieve such seamless movement.
Minimize Unnecessary Transportation with Shoplogix’s Smart Factory Suite
Like a savvy logistics manager, Shoplogix’s Smart Factory Suite optimizes the production flow and layout, ensuring that products and materials move through the manufacturing process in the most efficient way possible.
Let’s consider a simple example. Suppose a factory manufactures car parts. The current production flow involves transporting the parts across the factory for different stages of production – from shaping to polishing to packaging. This not only consumes time but also increases the risk of damage during transportation.
By implementing Shoplogix’s Smart Factory Suite, the factory can restructure its production flow and layout. For instance, stages that can be performed in close proximity, like shaping and polishing, can be located near each other. This reduces the distance the parts have to travel, minimizing unnecessary transportation.
Final Thoughts
Lean manufacturing, much like the methodology we discussed at the outset, is about constantly striving for better processes and outcomes. By focusing on these seven key areas, we embark on a path of ongoing refinement and excellence, reflecting the core principles of lean manufacturing in every step we take.
However, the key to successful implementation lies in leveraging advanced tools like Shoplogix’s Smart Factory Suite. With its real-time monitoring, intelligent planning, quality management, and advanced analytics, Shoplogix provides a comprehensive solution for manufacturers aiming to implement lean principles and drive operational excellence. Embrace the future of manufacturing with Shoplogix.
Transform your operations, reduce waste, and maximize productivity today.