Downtime is a manufacturing nightmare that costs businesses an average of $260,000 per hour, according to recent studies. It’s a persistent challenge that impacts productivity, efficiency, and profitability across various industries.
To combat this pervasive issue, it’s crucial to understand it’s root cause, its far-reaching effects, and the proven strategies to minimize its impact.
Definition and Characteristics
In Lean manufacturing, downtime refers to periods when production equipment or processes are not operating or functioning as intended, resulting in a temporary halt or reduction in output. In the context of lean manufacturing, downtime is considered a significant form of waste that negatively impacts productivity, efficiency, and profitability. However, it’s important to recognize that it’s not inherently bad; it can be beneficial for personal well-being and productivity, allowing for necessary rest and opportunities to engage in creative or productive activities.
Different Types of Downtime in Lean Manufacturing
Unplanned Downtime: This is the result of an unexpected equipment malfunction, system failure, or breakdown, leading to an unscheduled stoppage in production.
Planned Downtime: This includes scheduled stoppages for activities such as preventive maintenance, changeovers, and beginning-of-shift production meetings. While planned, these activities still contribute to it and should be minimized.
Little Downtime: Even small amounts of time spent not working due to minor issues or inefficiencies can accumulate and significantly impact overall productivity.
Needed Downtime: Time spent not working that is necessary for personal or professional well-being, such as breaks or training, is considered a form of downtime in lean manufacturing. However, it is recognized as essential for maintaining a productive and motivated workforce.
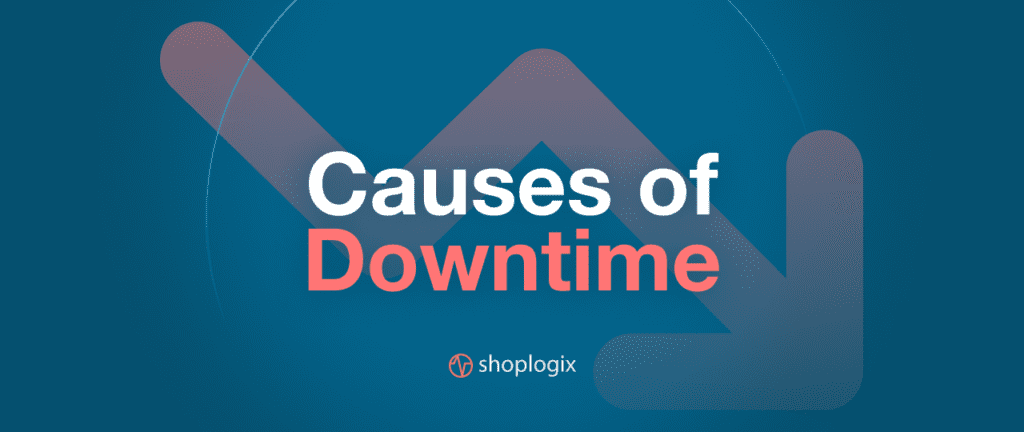
3 Common Causes of Downtime
Downtime in lean manufacturing operations can stem from various causes, which can be broadly categorized into three main areas: technical issues, human errors, and external factors.
1. Technical Issues
Equipment Failures or Breakdowns: Malfunctions or failures of production machinery, tools, or systems can lead to unplanned stoppages. Equipment failures can include issues with specific devices like a card reader, which may experience periods of unproductivity or malfunction.
Lack of Preventive Maintenance: Neglecting regular maintenance and upkeep of equipment increases the likelihood of breakdowns and unplanned downtime.
Hardware or Software Issues: Problems with the hardware or software components of production systems, such as control systems or automation software, can cause negatively impact on operations.
System Failures: Failures in critical systems, such as power supply, compressed air, or computer networks, can have a serious impact on production, particularly in industries that rely on continuous operations.
2. Human Errors
Operator Errors or Lack of Training: Mistakes made by operators due to inadequate training, lack of experience, or inattention can result in production stoppages and downtime.
Constant Distractions: A state of being constantly interrupted or diverted from one’s focus can lead to human errors and contribute to downtime.
Personal Emotional Needs: The personal needs and feelings of individuals, such as stress, fatigue, or personal issues, can affect their performance and lead to errors that cause downtime. Employees have their own emotional needs that need to be considered to maintain a healthy work-life balance.
3. External Errors
Changeovers or Setups: The time required for changeovers, such as switching between different product lines or adjusting equipment for new production runs, contributes to planned downtime.
Material Shortages or Quality Issues: Insufficient or defective raw materials, components, or supplies can disrupt production and lead to unplanned downtime.
Unplanned Maintenance or Repairs: Unexpected maintenance or repair work that arises due to unforeseen circumstances can result in unplanned downtime.
Inherently Negative or Crisis Events (Quarantine Downtime): External factors that are inherently negative or undesirable, such as natural disasters, power outages, or supply chain disruptions, can cause downtime and impact production.
What are the Effects of Downtime for Manufactuers?
Downtime can have severe consequences for lean manufacturing operations, both from a financial and operational standpoint.
Financial Impact
In the manufacturing industry, the cost of downtime is approximately $260,000 per hour. The average hourly wage earned by workers across the nation during it is a crucial factor to consider. Manufacturers experience approximately 800 hours of downtime every year due to maintenance, tool breaks, adjustments, etc.
Operational Consequences
Business Losses and Contract Defaults: Corporations can potentially lose business or default on contracts due to network outages or prolonged downtime, resulting in significant financial losses and damage to their reputation.
Reputational Impact: It can negatively impact companies from a reputational perspective, as customers may perceive them as unreliable or unable to meet their commitments. This can lead to a loss of trust and loyalty, ultimately affecting future business prospects.
Disruption to Production Flow: It disrupts the continuous flow of production, which is a fundamental principle of lean manufacturing. This disruption can lead to inefficiencies, waste, and a ripple effect throughout the entire manufacturing process.
Reduced Productivity and Output: Periods of downtime directly translate to reduced productivity and output, as resources (machinery, labor, materials) are not being utilized effectively during these times.
Inefficient Resource Utilization: It results in an inefficient use of resources, such as materials, labor, and energy, as these resources are idle and not contributing to value-added activities.
Decreased Overall Equipment Effectiveness (OEE): It negatively impacts OEE, a key metric in lean manufacturing that measures the overall performance and efficiency of production equipment and processes.
Strategies How Manufacturers can Minimize Downtime
Strategy 1: Implement Total Productive Maintenance (TPM)
Adopt a comprehensive TPM program to ensure optimal equipment reliability and performance. TPM involves:
- Preventive maintenance schedules to avoid breakdowns.
- Autonomous maintenance by operators for basic care.
- Training to build maintenance skills across the workforce.
- Implementing a new procedure involving a robotic arm.
Strategy 2: Streamline Changeovers and Setups
Reduce it from changeovers and setups by:
- Applying SMED (Single Minute Exchange of Die) principles.
- Performing parallel operations where possible.
- Providing proper training and standardized procedures.
Strategy 3: Optimize Material Planning and Inventory Management
Prevent it due to material shortages by:
- Accurate demand forecasting and production planning.
- Maintaining optimal inventory levels with just-in-time practices.
- Developing robust supplier relationships for reliable deliveries.
Strategy 4: Leverage Manufacturing Execution Systems (MES)
Utilize MES software from Shoplogix to:
- Enable real-time production monitoring and control.
- Gain data-driven insights for schedule optimization.
- Quickly adapt to changing conditions and minimize disruptions.
Strategy 5: Foster a Culture of Continuous Improvement (CI)
Encourage a mindset of continuous improvement (Kaizen) by:
- Empowering employees to identify and address inefficiencies.
- Conducting regular kaizen events and root cause analysis.
- Implementing visual management for increased transparency.
Employees can also contribute to open-source communities, helping to create a more sustainable world.
Strategy 6: Ensure Proper Training and Skill Development
Invest in comprehensive training programs to:
- Build operator competencies and reduce human errors.
- Develop maintenance skills across the workforce.
- Foster a culture of accountability and ownership.
How to Measure and Analyze Downtime for CI
Effective factory scheduling goes hand-in-hand with proactively measuring and analyzing downtime to identify areas for improvement and drive continuous optimization. This data-driven approach is crucial for maximizing productivity and efficiency.
Key Performance Indicators (KPIs)
Manufacturers should track key metrics related, such as:
Unavailability: This KPI measures the proportion of time that a system, equipment, or production line is unavailable or offline due to downtime.
Downtime Percentage: Service level agreements often specify a maximum acceptable percentage value for allowable downtime, making this a critical KPI to monitor.
Data-Driven Insights
By consistently measuring and analyzing downtime data, organizations can gain valuable insights to:
Improve Overall Equipment Effectiveness (OEE): Downtime is a key factor impacting OEE, a crucial metric for measuring productivity in lean manufacturing. Reducing it can significantly boost OEE.
Identify Root Causes: Detailed downtime data enables root cause analysis, pinpointing specific issues like equipment failures, material shortages, or process inefficiencies that contribute to unplanned stoppages. Analyzing it data can also help organizations prepare for the next crisis.
Optimize Schedules: With a clear understanding of downtime patterns and causes, manufacturers can optimize production schedules, allocate resources more effectively, and implement targeted improvement initiatives.
To gain these insights, manufacturers can leverage external monitoring services and tools to track uptime, downtime, and availability of critical systems, equipment, and processes in real-time. This data, combined with advanced analytics capabilities like those offered by Shoplogix, empowers manufacturers to make data-driven decisions and drive continuous improvement in factory scheduling and overall operational efficiency.
What You Should Do Next
Explore the Shoplogix Blog
Check out our other blog posts. It’s full of useful articles, professional advice, and updates on the latest trends that can help keep your operations up-to-date. Take a look and find out more about what’s happening in your industry. Read More
Request a Demo
Learn more about how our product, Smart Factory Suite, can drive productivity and overall equipment effectiveness (OEE) across your manufacturing floor. Schedule a meeting with a member of the Shoplogix team to learn more about our solutions and align them with your manufacturing data and technology needs. Request Demo